Logistics Management: Best Practices for a Flawless Shipping Process
June 21st, 2019 | 6 min. read
By Peggy Sawyer
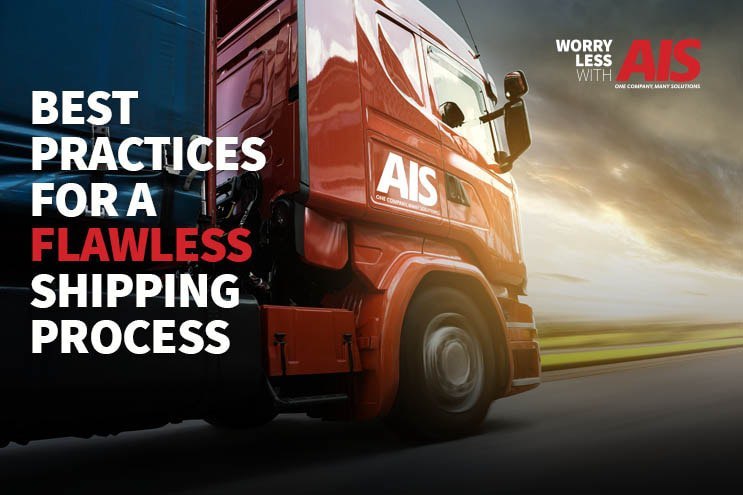
READ TIME: 6 MINS.
What shipping processes does your business have in place, and how do you continually implement them within your logistics department? Maybe you’ve noticed a number of incorrect, fulfilled orders, or missing inventory, leaving you wondering, “How do I fix this?”
When it comes to shipping and logistics management, it’s imperative to have an exceptionally organized warehouse, and well-trained employees, so your customers are receiving what they ordered in an accurate and timely fashion.
Your employees are the ones in charge of fulfilling and processing orders, right? So, even the slightest bit of miscommunication could result in a very unhappy customer, which is the last thing any business wants.
Before we dive in and explore some of the best practices for a flawless shipping process, let’s first go over what logistics management is.
Techopedia says, “Logistics management is a supply chain management component that is used to meet customer demands through the planning, control, and implementation of the effective movement and storage of related information, goods and services from origin to destination. Logistics management helps companies reduce expenses and enhance customer service.
The logistics management process begins with raw material accumulation to the final stage of delivering goods to the destination…”
To sum that up, your role as a logistics or shipping manager, or employee, is to organize the storage and distribution of the products or services you sell. Believe it or not, even companies who don’t sell an actual commodity, but more of a service, have logistics management.
Speaking of services, ever heard of Managed IT Services, and how they can help you achieve business growth? Read our article to learn more, What is Managed IT Services? How to Tell If You Need Them.
Follow along as we give you some of the best practices to implement within your organization that will take your logistics to the next level, allowing you to focus on other parts of your business, like closing deals!
Logistics Management: What Steps Should I Take?
With any process, comes steps. One of the best and most important ways to encourage communication, understanding, and accuracy between your employees is to have procedures and guidelines, demonstrating how your logistics should operate each day, even when a problem arises.
The steps to take for logistics management varies depending on what your business is selling, and shipping, as well as how large or small your customer base is. However, practicing these general shipping rules and guidelines will get just about any company on the right path to success.
Inventory Checks Are A Must
You’d be surprised how many companies never perform routine inventory checks. Who has the time to lose or money to waste by shutting down their warehouse for a couple of days so they can count every product?
We understand the frustrations and fears of performing routine inventory checks. However, it’s imperative to do so if you’re truly dedicated to improving your business’ logistics management and shipping options and processes.
One of the critical aspects of inventory management is that it gives you a much better understanding of what you have and where it’s located in your warehouse. Not to mention, being in control of your inventory allows you to know when product is going in and out, helping to lower costs, speed up fulfillment, and prevent theft.
Conducting routine inventory checks is also essential to maintaining a healthy balance of stock in your warehouse, especially if you have more than one warehouse. It would feel pretty defeating to lose a sale simply because you didn’t have enough inventory to fulfill an order to meet the customer's needs.
Even with a strong customer base, constant inventory or logistics management issues can drive even your most loyal customer away.
As far as the frequency of inventory checks, that’s really up to you. Most businesses follow a bi-annually, or quarterly inventory check— rarely is it a good idea to check inventory once a year.
Try working with your team on finding a good time to pause the shipping processes of your warehouse momentarily. It could even be early in the morning before the workday begins, or a weekend day. No, it's not ideal, but two times a year won’t kill ya’!
So, the takeaway? When you have control over the products you sell, you’re able to provide a customer experience that your competition simply cannot.
By the way, providing a great customer experience is a little different than providing customer service. Read our article to learn more, Customer Experience: How to Achieve SMB Growth and Slay the Giants.
Location and Transportation Management For All Warehouses
Earlier, we briefly mentioned the importance of inventory control, especially if your business has more than one warehouse. Some companies even have warehouses around the world, making it challenging, yet necessary, to have an almost-perfect logistics management process.
The following steps are great to take and implement throughout all your locations, to ensure each warehouse is consistent and follows the same processes as all the others.
- Database accuracy: Once your warehouse receives the product, it must be entered into your inventory database at the time of delivery. By doing so, you’ll quickly eliminate the chances of product going missing, or ending up in the wrong location of your warehouse. The same goes for when the product leaves. Whether your database is more manual, or almost one hundred percent automatic, make sure all products that enter and leave your warehouse are accounted for.
- Bin locations: If the products in your warehouse include many small or complex parts, use a system to organize them, such as labeled bins. Each part should have an item number, which belongs in the appropriate bin with that exact label number. Never include two parts together in the same bin or container, that’s just asking for a disorganization disaster. Within your database, you can enter where each inventory bin is located, making it easy to find the products you need when packing or assembling orders.
- Communicate: We can’t say this enough. It’s always important to communicate with your team no matter what department you manage, but communication for successful logistics management is something that can’t ever get overlooked. Each one of your staff members, at all of your warehouses, should always be able to get a hold of one another, and the communication lines must always be open when implementing new systems or products. In situations such as inventory control, overly communicating is even better, even if you think it’s too much. Your customers will notice.
Growing From Mistakes
Let’s face it, you and your employees aren’t perfect—no business is! There’s always going to be issues that come up and sometimes, they’re out of your control.
The key though is to do as much as you can to prevent the problems from occurring that you do have control over. And when that fails, come up with more detailed shipping solutions and materials handling guidelines.
At the beginning of this article, we asked if you’ve been noticing a number of orders being fulfilled incorrectly, or if there’s been an increase in the number of missing inventory. If you answered, “Yes,” don’t feel that you’re alone.
There are many businesses in your exact shoes. However, what makes you stand out is how you go about resolving the issues, as well as preventing them from happening again.
It may seem easier at times to ignore an issue after it’s resolved, and move on with your day. However, you’re only putting a band-aid on the situation, demonstrating you're not dedicated to figuring out why the problem happened in the first place.
For example, if your customers are continually angered because their orders are always wrong, or missing products, it’s time you figure out why. Start with your employees and review how they pack or assemble orders.
Maybe they’re doing something that’s interfering with the accuracy. More guidance might be needed for your employees to meet customer requirements, giving them the ultimate customer experience.
As you can tell, there’s a lot that goes into logistics management, and we’ve only brushed the surface! But, with the right mindset, knowledge, and resources, your business is on its way to having a flawless shipping process that your competitors won’t be able to compete with.
At AIS, we love providing tools and resources to our customers and readers so they’re able to grow their business in ways they might not have known prior. Achieving the goals you’ve set in place is important to you, and you’ve worked hard at doing so, which is why we are always eager to share with you some of our best practices. If you’d like to learn more about logistics management, or any of the products and services we offer, reach out to one of our business technology consultants, here. We’re here to give you peace of mind to help you win more business.
Peggy's been the copier business for over 20 years, worked as the Logistics Manager of AIS since 2004. On the weekends, she enjoys camping, boating, and off road riding with her family and dogs.
Topics: